Vesta I. Bateman
Chair, IEST Working Group DTE032
The IEST Recommended Practice on pyroshock testing has been revised and updated to reflect advances in the art of pyroshock testing and to address common problems related to data accuracy in the pyroshock community. The key changes to IEST-RP-DTE032: Pyroshock Testing Techniques are described here.
New definitions for near-field pyroshock, mid-field pyroshock, and far-field pyroshock adopted by IEST-RP-DTE032.2 are consistent with the definitions given in MIL-STD-810G, Method 517, as shown in the table and the spectra definitions below. The definitions and table values are quantified in terms of shock response spectra (SRS). The SRS, with an appropriate damping value, is the most widely used tool to analyze pyroshock data and is calculated using acceleration measurements near components and subsystems that must be qualified separately. The Jet Propulsion Laboratory will be revising NASA-STD-7003 during the coming year, and the current NASA values for near-field, mid-field, and far-field pyroshock are also shown in the table.
A near-field pyroshock test requires frequency control up to and above 10 kHz for amplitudes greater than 10,000 g. A pyrotechnically excited simulation technique is usually appropriate, although in some cases a mechanically excited simulation technique may be used.
A mid-field pyroshock test requires frequency control from 3 kHz to 10 kHz for amplitudes less than 10,000 g. A mechanically excited simulation technique other than shaker shock is usually required.
A far-field pyroshock test requires frequency control no higher than 3 kHz for amplitudes less than 1,000 g. A shaker shock or a mechanically excited simulation technique is appropriate.
COMPARISON OF CURRENT SHOCK RESPONSE SPECTRA PYROSHOCK DEFINITIONS
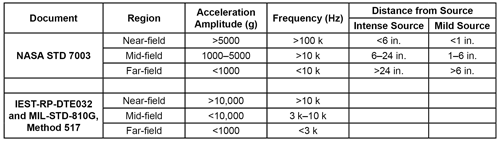
IEST-RP-DTE032.2 contains a new section on pyroshock variability; this variability is quantified in terms of SRS. Opportunities to make multiple detonations of pyrotechnic devices with the same structure are rare. Pyroshock is by its nature highly variable or unrepeatable, but in many cases program decisions are based on one pyroshock data set. The reason for this is usually cost, but there is also a very real problem in the timing and availability of actual complete system hardware and components. That is, a new program typically begins with a set of new requirements for components and complete system performance. A portion of the complete system is assigned to an individual or groups of engineers for development. So what pyroshock requirements do the engineers use? A conventional practice is to use requirements for another complete system that are “considered similar” to the new system. This approach may be justified in the early stages of a program, but later in the program as components and subsystems mature, more realistic specifications must be created. At this point, a mock system may be constructed and used for detonation of actual pyrotechnic devices; the quality of the mock system components greatly affects the nearby acceleration measurements and consequently, the accuracy of the resulting SRS specifications. This is evident with simple structures as well as complex structures. The RP includes two examples of the variability of pyroshock to emphasize the unrepeatability of pyroshock and to provide a basis for the +6 dB tolerance and +3-6 dB margins typically added to pyroshock specifications. The availability of these data sets of multiple pyroshock measurements is relatively recent and provides new insight into the pyroshock phenomena.
Three new resonant techniques for pyroshock simulation have been added to the RP:
- Full-scale or complete system tests with a resonant fixture
- Three-axis pyroshock simulations for mid-field pyroshock
- Three-axis pyroshock simulations for near-field pyroshock
For full-scale tests, the pyrotechnic source and a portion of the adjacent structure may be replaced by a resonant plate or fixture designed so that the first mode of the plate or fixture corresponds to the dominant frequency produced by the pyrotechnic device and the associated structure. The resonant plate or fixture should be attached to the test structure in a manner that simulates the mechanical linkage of the pyrotechnic source. When this attached plate or fixture is excited into resonance by a mechanical impact, the response of the plate or fixture should provide the desired input to the test structure. A resonant fixture has successfully simulated three-axis component shock response spectra with one impact to the resonant fixture for frequencies up to 4 kHz on a full-scale weapon structure weighing 400 lb and also may be used for satellite structures. This test configuration is a major step toward eliminating over-testing in mechanical simulation of pyroshock that creates unrealistic mechanical failure of the unit under test.
Over-testing occurs because all pyroshock resonant fixture simulations described in the previous edition of the RP require that the test item be attached to the fixture and tested in three separate axes. Also, all pyroshock simulation methods have some cross-axis response in addition to the intended in-axis response, so over-testing of the test item routinely occurs. However, in some cases all three axes may be tested with one impact on a thick resonant fixture to simulate mid-field pyroshock or near-field pyroshock. These fixtures must be designed for the specific test requirement and for specific, small test items. Time history magnitudes of 1000 g to 80,000 g with knee frequencies in excess of 15 kHz have been obtained and are demonstrated in the figures in IEST-RP-DTE032.2 as both acceleration time-histories and positive and negative shock response spectra calculated in one-sixth octave bands. Again, these test configurations are a major step towards eliminating over-testing in mechanical simulation of pyroshock that creates unrealistic mechanical failure of the unit under test. Additionally, the cost of the pyroshock simulations described above are significantly less, and the tests are more repeatable than testing with the detonation of pyrotechnic devices.
Finally, IEST-RP-DTE032.2 includes a new section on corrupted pyroshock data. Recent events in the pyroshock testing community have shown that corrupted pyroshock data are still being taken at government agencies and private companies. In one case, upon request, I analyzed a set of corrupted data. The sources of data corruption and contamination appeared to be the usual culprits that have been known for some time: digital aliasing and offsets in the data. The remedies for these problems are readily available, so why are corrupted pyroshock data still acquired? In response to reviewers of the RP in the pyroshock community, this section was added and describes practices that cause corrupted pyroshock data and recommendations for acquiring uncorrupted data.
Vesta I. Bateman, a mechanical shock specialist, is Chair of IEST Working Group DTE032 and a Senior Member of IEST. She established her firm, Mechanical Shock Consulting, Albuquerque, New Mexico, after retiring from Sandia National Laboratories. During her 28 years at Sandia, Bateman was the Facility Leader for the Mechanical Shock Lab, where she developed a unique shock isolator for a high-shock, high-frequency accelerometer. Bateman received IEST’s Edward O. Szymkowiak Award in 2003 for her leadership in pyroshock testing. A widely published, award-winning author, she holds a PhD from the University of Arizona.
© 2009 IEST All rights reserved
Order your copy of IEST-RP-DTE032.2